亲和聚结法中过滤元件的孔径将决定分离效果的好坏。如果材料的孔径较大,则许多小直径的油滴将无法被分离出来。然而,也没有必要把材料的孔径做得太小,这主要是因为随着被过滤出来的大油滴在过滤材料上的聚结,元件材料孔径的有效流通面积被明显减小,从而可使更小直径的油滴被分离出来。
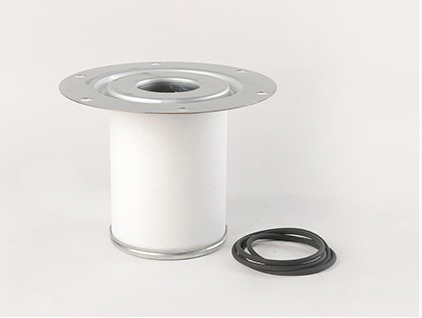
在早期的设计中,曾采用纯羊毛、改性化纤织物,以及烧结金属和陶瓷作为亲和聚结法的过滤元件材料。近年来,已普遍采用专门为此用途开发的超细玻璃纤维等材料,取得了除油效果佳、寿命长、压降小的效果。通常这类过滤元件可使气体中的含油量降至ppm级。
但无论这种过滤元件的结构多么复杂,经其分离后的气体中仍会含有某些润滑油。这是因为机械碰撞法和亲和聚结法,都无法把处于气相的润滑油有效地分离出来。
利用活性碳元件的吸附作用,经过吸附后的气体含油量,甚至比普通大气环境中的含油量要低很多。这些过滤元件往往不具备自净功能,油气混合物中的灰尘等杂质进入元件后,会滞留其中。所以,在运行过程中,过滤元件的压降逐渐增大。当压降过量时,就需要更换过滤元件。为了尽可能减少气体流过过滤元件时的压力损坏和提高分离效果,气体在其间的流速不能太高。然而,流速越低,所需的过滤材料就越多,过滤元件的成本就越高。
合理的压降和流速,与被压缩介质的密度和润滑油的黏度等因素有关。一般通过洁净过滤元件的压降为0.025~0.03mpa,当此压降增加到0.07~0.1mpa时,就需更换过滤元件。对于,气体流过过滤元件时的速度应在 0.1m/s 左右。